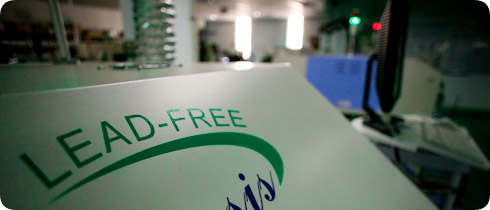
Longjoin is lead-free
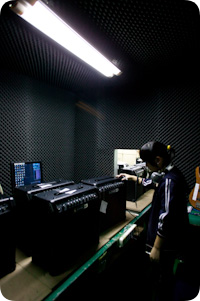
Operator doing hearing test in hearing chamber.
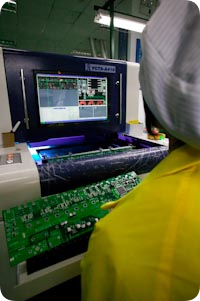
Operator inspecting PCBA with AOI.
Quality Control Methodology
Longjoin make use of a number of quality control tools to ensure the incoming materials, process and finished goods in good quality. They are namely,
FAI
Online Self-checking
Major Inspection
IPQC
End Item Inspection
Final Inspection
Traveler and Labeling
FAI (First Article Inspection)
- First articles of every shift or whenever operators change takes place
- To avoid whole lot failure
- Find out problems at the earliest stage
-
Triple inspection
operation's self-checking
Line foreman's checking
Inspector's inspection
Online Self-checking
- Operators check their own our works from time to time during productions
- Find out problems at the earliest stage
- Help operators better understand the standards
Major Inspection
- For some major inspection items, 100% full check will be applied
- Major inspection items - potential failures causing impact to safety, function and assembly structure
- Dedicated inspectors or fixtures would be used
IPQC (In-Process Quality Control)
- In production random check
- To find out problems caused by operators, machines, tools and process
- Indentify problems at the operation level
End Item Inspection
- Essential for parts made by moldings and fixtures
- Inspecting the last item of the mass production
- To ensure moldings and fixtures in good conditions after a run
- Done collaboratively by operators and inspectors
Final Inspection
- The final keeper – preventing NG from going out
- Completion of batch of F/G
- Sampling or full check
Traveler and Labeling
- Traveler to keep track of the operator, inspector, date, shift, serial number, etc.
- Various labels, categorized in different colours, to identify materials, sub-aseemblies and goods in different stages
Quality Certifications and Continuous Improvement at a Glance
-
ISO9001:2008
Acquired ISO9001:2008, Longjoin operates fully following ISO9001 system
-
UL, CE, 3C
Have successfully passed UL, CE and 3C audits and qualified as UL, CE and 3C products maker
-
IPC-A-610
Inspection standard used is based on customer requirements and following IPC-A-610
-
RoHS Implementation and Control
RoHS implemented in the areas of incoming materials control, production process, facility, test and inspection
-
PDCA
P (Plan) – planning based on customer requirement
D (Do) – do the work per the plan
C (Check) – check the goods and process per the plan
A (Act) – analyze and continuous improve
Use PDCA as a tool to monitor and solve quality issues
-
Quality Improvement Team
Formed to push for continous quality improvment with team members – from operators to General Manager
Statistical analysis and PDCA are useful tools